Recently, a research team led by Prof. YE Hong from the University of Science and Technology of China (USTC) developed a alumina ceramic bionic wick with finger-like pores inspired by the stomatal array of natural leaves. Their research was published Langmuir. The paper was selected as an Editors’ Choice by the American Chemical Society (ACS) and was featured as a headline on their website.
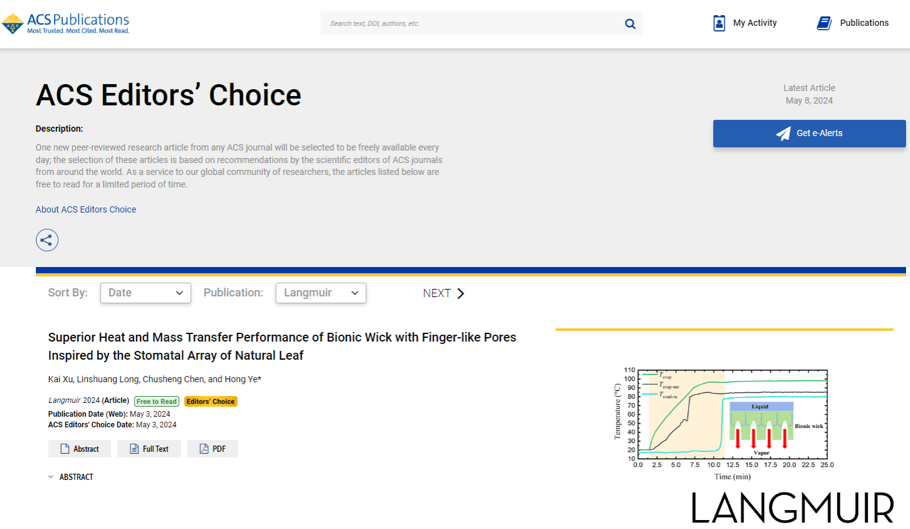
The team’s work selected as ACS Editors’ Choice. (Image by USTC)
As the performance of electronic chips continues to improve, their power consumption also increases, posing new challenges for cooling strategies. Loop heat pipes (LHPs) are an compelling cooling solution due to their high heat transfer capability, antigravity heat transfer, and absence of moving parts. However, the differing requirements for flow resistance and capillary force make designing the pore structure of the capillary wick within an LHP challenging. Specifically, larger pores are needed for gaseous working fluids to reduce flow resistance, while smaller pores are necessary to provide sufficient capillary force for liquid suction.
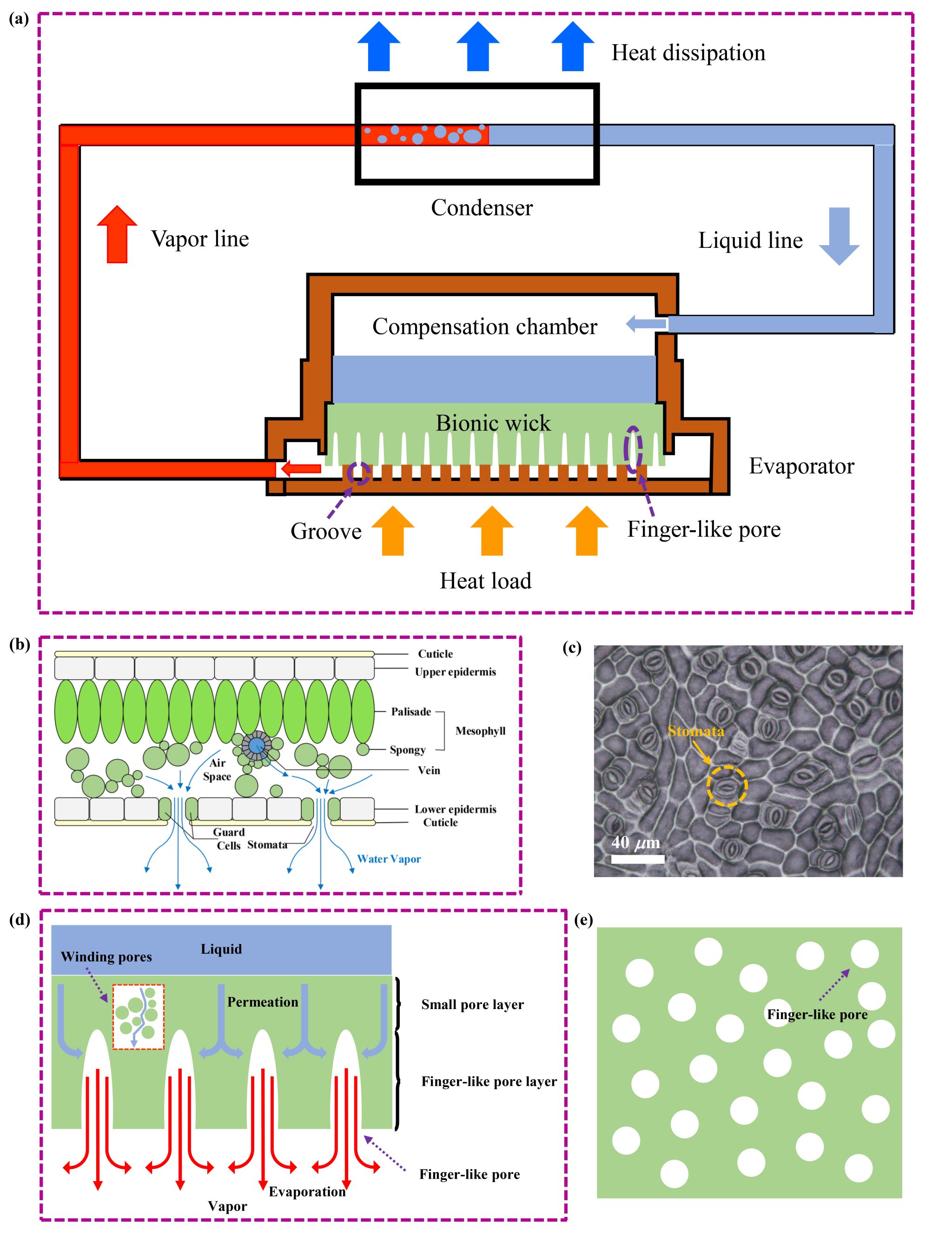
Design idea of the bionic wick. (Image by Prof Ye’s team)
To address this dilemma, Prof. YE Hong’s team drew inspiration from the stomatal structure of plant leaves. Using phase inversion tape casting, they successfully developed an alumina ceramic bionic wick with finger-like pore structures. These finger-like pores, similar to the stomatal structure of plant leaves, effectively increase the gas-liquid interface area, allowing for the timely expulsion of gaseous working fluids and reducing mass transfer resistance. Simultaneously, the micron-sized pores around the finger-like pores provide sufficient capillary force to replenish liquid at the gas-liquid evaporation interface. Start-up and operation tests of the LHP confirmed the superior heat and mass transfer performance of the bionic wick.
This work not only resolves the conflict between enhancing capillary force and reducing flow resistance, but also offers a novel solution for high-power-density electronic chip cooling. It shows potential application value in efficient thermal management for aerospace, aviation, and microelectronics fields.
Paper Link: https://pubs.acs.org/doi/10.1021/acs.langmuir.4c00434
(Written by LI Rui, edited by ZHANG Yihang, USTC News Center)